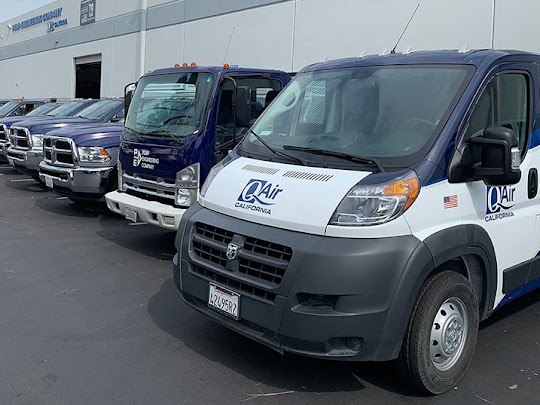
Preventative maintenance and prompt part replacement are key to maximizing the efficiency and life of your industrial air compressor. Compromising on maintenance or repairs leads to reduced performance, increased energy usage, breakdowns, and ultimately higher production costs and losses.
The services we provide in Imperial County can help our clients avoid such breakdowns by scheduling regular service of your industrial equipment.
As one of the most recognized service companies for industrial air compressors in Imperial County, Q Air-California has the expertise, experience, and equipment needed to service, repair, and maintain an optimal air compressor system.
Q Air-California specializes in providing our Imperial County clients with cost effective service, repair, & maintenance solutions for industrial air compressor systems. With a combination of cutting-edge equipment and nearly 20 years in the industry, our air compressor services are renowned across Imperial County and the State of California due to their efficiency, longevity, and continued support for the lifetime of your machinery.
Our engineers and technicians are always prepared and on standby to respond quickly to any equipment-related failures and other emergencies. In the event of an unforeseen breakdown, we are available to get your compressors going again as soon as possible to reduce the impact in your bottom line.
Industries We Service In Imperial County
- Aerospace
- Automotive
- Low Pressure
- Manufacturing
- Breathing air
- Carpet
- Chip Manufacturing/Electronics
- Climate Control
- CNC routing tables
- Contractor / Builder
- Distribution/Logistics
- Energy Exploration
- Food & Beverage
- Government
- Hospitals
- Material Handling
- Medical & Dental Labs
- Motion Pictures
- Municipalities
- Oil & Gas
- Paint/Rubber
- Pharmaceutical
- Plastics
- Processing Facilities
- Repair Facilities
- Woodworking
Our industrial air compressor services are available to clients across Imperial County. We cater to all makes and models available in California. You can be assured that our team will repair any compressor breakdown quickly, efficiently, and with less downtime compared to other service providers, and protect you against unforeseen problems. Contact us at 888.311.7247 today!